Construction Management Solution.
Project Initiation & Planning
1. Project Kickoff & Stakeholder Alignment
- Conduct stakeholder workshops to define objectives, scope, and success criteria
- Identify key roles & responsibilities (RACI matrix)
- Establish communication protocols and reporting structures
2. Scope Definition & Work Breakdown
- Develop detailed project charter with deliverables
- Create Work Breakdown Structure (WBS)
- Define milestones and critical path

3. Schedule & Resource Planning
- Build baseline project schedule (Gantt/P6/MS Project)
- Allocate human/resources/budget requirements
- Optimize resource leveling to prevent bottlenecks
4. Risk & Compliance Framework
- Conduct risk identification workshops
- Develop risk register with mitigation strategies
- Ensure regulatory/compliance alignment
5. Approval & Governance Setup
- Prepare project initiation document (PID) for sponsor sign-off
- Establish change control processes
- Implement project tracking dashboards
Design & Pre-Construction Management
1. Design Development & Coordination
- Conduct stakeholder workshops to finalize design requirements
- Prepare conceptual/schematic designs (architectural, structural, MEP)
- Coordinate multi-disciplinary design teams (architects, engineers, specialists)
- Ensure compliance with local codes, zoning laws, and sustainability standards
2. Design Documentation & Review
- Develop detailed construction drawings (CAD/BIM models)
- Review design deliverables for accuracy, constructability, and value engineering
- Manage design revisions based on client/authority feedback
- Prepare tender/construction-ready documents
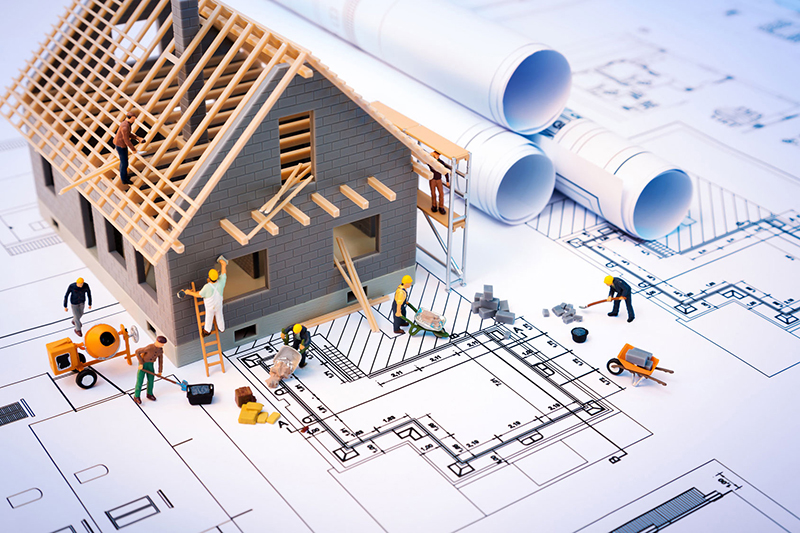
3. Permitting & Regulatory Approvals
- Identify required permits and approvals (building, environmental, utility)
- Liaise with authorities (municipalities, fire departments, DISCOs)
- Track approval timelines and resolve compliance issues
4. Contractor Prequalification & Tendering
- Prepare technical specifications and BOQ
- Shortlist qualified contractors/vendors
- Manage bid process, evaluations, and negotiations
- Recommend award strategies
5. Pre-Construction Planning
- Finalize project schedules, budgets, and procurement plans
- Conduct constructability reviews and risk workshops
- Establish quality/safety protocols
- Develop stakeholder handover plans
Construction Execution Management
1. Construction Planning & Mobilization
- Finalize baseline schedules, budgets, and resource plans
- Oversee site mobilization (logistics, temporary facilities, permits)
- Conduct pre-construction meetings with contractors and stakeholders
- Implement digital project management tools (BIM, ERP, drones)
2. On-Site Supervision & Quality Control
- Monitor daily progress vs. schedule (Gantt/P6 updates)
- Enforce QA/QC protocols (material testing, workmanship standards)
- Conduct regular site inspections (safety, compliance, productivity)
- Manage non-conformance reports (NCRs) and corrective actions
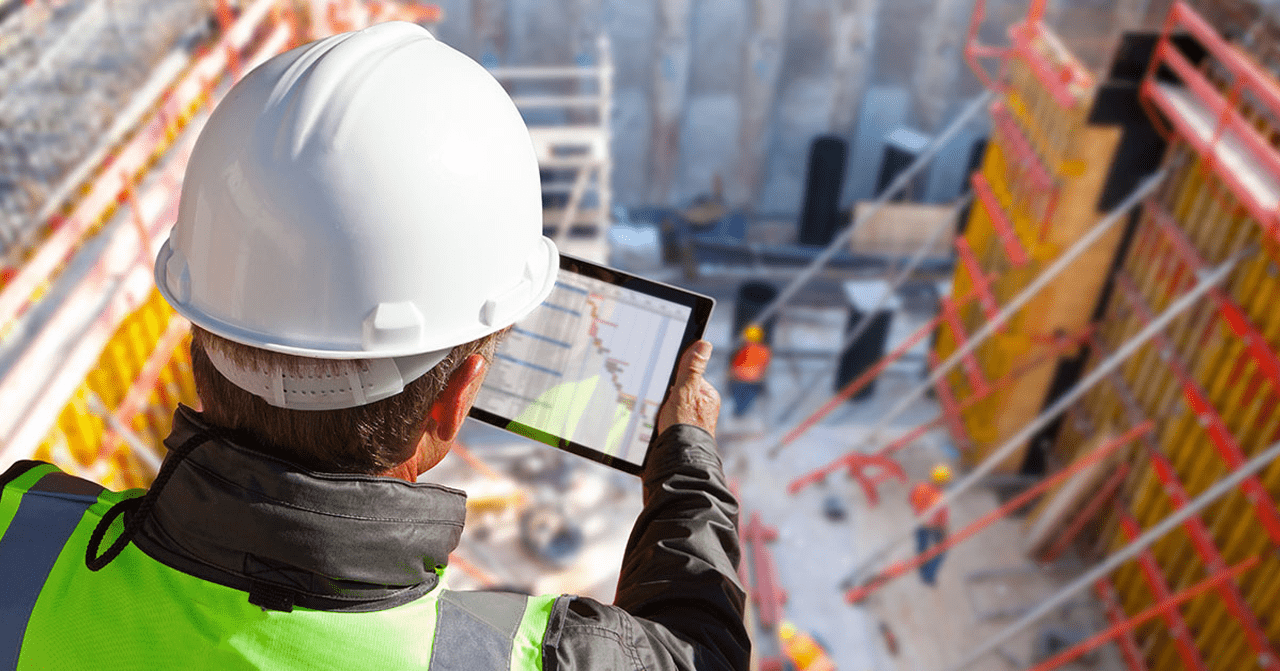
3. Contractor & Subcontractor Coordination
- Chair weekly coordination meetings (RFIs, change orders, delays)
- Track subcontractor performance (timeliness, quality, safety)
- Resolve disputes and claims through documented processes
- Ensure adherence to contractual obligations
.
4. Cost & Change Management
- Monitor actual vs. budgeted costs (labor, materials, equipment)
- Evaluate change order requests (impact on time/cost/scope)
- Approve progress payments against milestones
- Optimize resource allocation to prevent overruns
5. Safety & Compliance Oversight
- Enforce OSHA/local safety regulations (PPE, permits, training)
- Conduct emergency drills and safety audits
- Ensure environmental compliance (waste disposal, emissions)
- Maintain statutory inspection records
6. Reporting & Stakeholder Communication
- Issue daily/weekly/monthly progress reports
- Update real-time dashboards (KPIs, risks, issues)
- Present executive summaries to clients/investors
- Document lessons learned for continuous improvement
Vendor & Contract Management
1. Vendor Pre-Qualification & Selection
- Develop vendor evaluation criteria (technical, financial, compliance)
- Conduct market research to identify potential suppliers/contractors
- Manage RFQ/RFP processes (bid documentation, timelines, clarifications)
- Perform due diligence (background checks, site visits, reference validation)
2. Contract Development & Negotiation
- Draft contract terms & conditions (scope, deliverables, SLAs, penalties)
- Negotiate pricing, payment terms, and warranties
- Define KPIs and performance metrics for vendor accountability
- Ensure regulatory and legal compliance (tax, labor, safety laws)
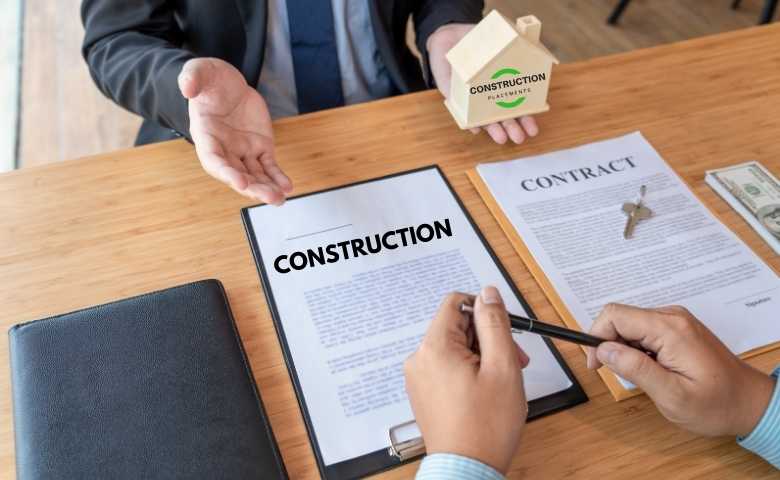
3. Contract Execution & Monitoring
- Maintain centralized contract repository with key dates and obligations
- Track vendor performance (quality, timelines, cost adherence)
- Conduct regular review meetings (progress, issues, improvements)
- Manage change orders and amendments
4. Risk & Dispute Management
- Identify contractual risks (delays, cost overruns, non-compliance)
- Implement mitigation strategies (penalties, liquidated damages)
- Resolve disputes/claims through mediation or arbitration
- Enforce exit/clause strategies for underperforming vendors
5. Relationship & Performance Optimization
- Develop vendor scorecards (quarterly/annual evaluations)
- Facilitate collaboration workshops for continuous improvement
- Recommend strategic partnerships for long-term cost savings
- Conduct contract closeout reviews (lessons learned, feedback)
Technology & Innovation Integration BIM
(Building Information Modeling)
1. BIM Strategy & Implementation Planning
- Conduct BIM maturity assessment & gap analysis
- Develop BIM execution plan (BEP) aligned with project goals
- Define LOD (Level of Detail) requirements for each phase
- Establish collaboration protocols for stakeholders
2. BIM Model Development & Coordination
- Create 3D parametric models (Architectural, Structural, MEP)
- Conduct clash detection and resolution (Navisworks, Revizto)
- Generate 4D (time) & 5D (cost) simulations
- Integrate GIS, IoT, and facility management data
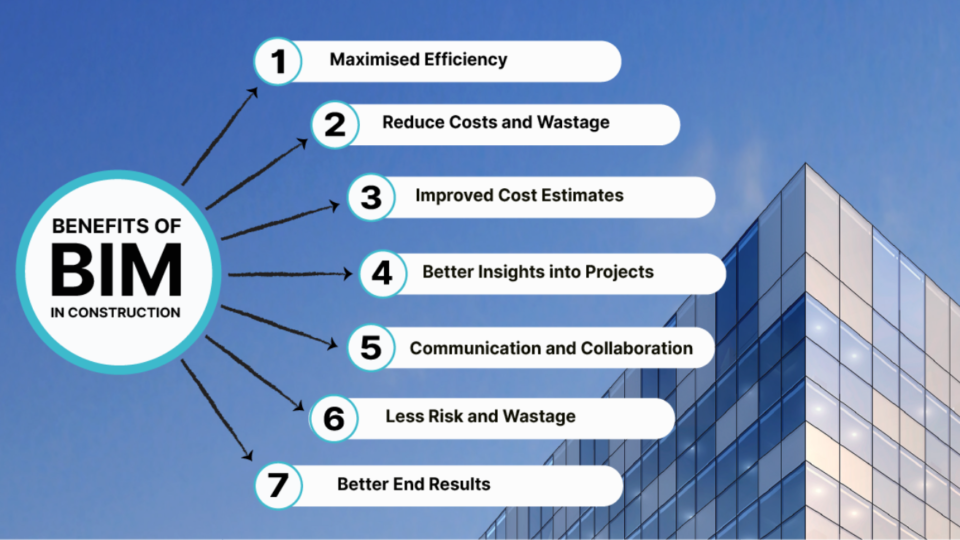
3. Digital Collaboration & Workflow Optimization
- Implement Common Data Environment (CDE) for centralized access
- Set up BIM 360/ACC platforms for real-time collaboration
- Train teams on model-based workflows
- Automate QA/QC checks using AI/ML tools
4. Innovation Integration
- Deploy AR/VR for design reviews & client presentations
- Enable digital twin for asset lifecycle management
- Integrate scan-to-BIM for as-built verification
- Pilot generative design & AI-driven optimization
5. Performance Monitoring & ROI Analysis
- Track BIM adoption metrics (RFIs reduced, clash savings)
- Calculate time/cost benefits vs. traditional methods
- Provide innovation roadmaps for future projects
- Conduct post-implementation reviews
Project Closeout & Handover
1. Closeout Planning & Documentation Review
- Develop closeout checklist aligned with contract requirements
- Verify as-built drawings against final construction
- Compile O&M manuals, warranties, and guarantees
- Confirm regulatory compliance certificates (safety, environmental)
2. Defect & Punch List Management
- Conduct final inspections with contractors and clients
- Document outstanding works and defects
- Track punch list completion with responsible parties
- Verify corrective actions before handover
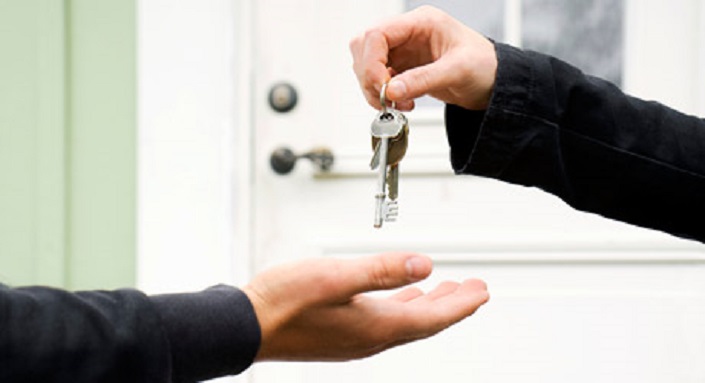
3. Financial & Contractual Closure
- Reconcile final accounts (retentions, variations, claims)
- Obtain lien waivers and release of securities
- Close subcontractor and supplier contracts
- Archive project financial records
4. Asset & System Handover
- Transfer digital models (BIM) and asset data
- Conduct training sessions for facility teams
- Hand over keys, access controls, and spare parts
- Provide emergency contact lists and escalation protocols
5. Lessons Learned & Performance Evaluation
- Facilitate closeout workshops with stakeholders
- Document successes, challenges, and improvement areas
- Prepare final project performance report (time, cost, quality)
- Recommend process optimizations for future projects
Post-Construction Support
1. Project Overview:
- Provide expert post-construction consultancy services to ensure smooth project closeout and operational readiness.
- Assist the client with inspections, quality assurance, system commissioning, documentation management, warranty coordination, training, and handover processes.
- Ensure that the project is fully compliant with construction specifications, contractual requirements, regulatory standards, and operational needs.
- Support the client in achieving a seamless transition from construction phase to occupancy and building operation phase.
2. Objectives:
- Facilitate a smooth handover of the project from construction to full operational status.
- Verify that all construction activities are completed according to design, quality, and regulatory standards.
- Ensure that all outstanding punch list items and warranty obligations are properly documented and addressed.
- Support the client’s facilities management and operations teams through detailed system training and documentation review.
- Minimize early-stage operational risks, maintenance issues, and defects through quality verification and early troubleshooting.
- Strengthen the client’s ability to manage their asset effectively with proper documentation, training, and post-occupancy support.

3. Scope of Services:
- Final Site Inspections and Quality Assurance Review:
- Conduct comprehensive final inspections of all completed construction work.
- Identify any incomplete works, defects, or quality concerns.
- Development and Management of Punch Lists:
- Create detailed punch lists based on inspections.
- Monitor and track the closure of all punch list items with contractors.
- Coordination of Deficiency Rectification:
- Facilitate communication between client and contractors/subcontractors to ensure timely resolution of deficiencies.
- Review and Handover of As-Built Drawings, Manuals, and Warranties:
- Collect, review, and organize as-built drawings, operation and maintenance (O&M) manuals, and warranty documents.
- Ensure completeness and accuracy of handover packages.
- Building Systems Testing, Commissioning, and Performance Verification:
- Oversee and verify testing, commissioning, and performance of all building systems (e.g., HVAC, electrical, plumbing).
- Training Sessions for Client’s Facilities Management Teams:
- Conduct detailed operational training for facilities staff covering systems operation, emergency procedures, and routine maintenance.
- Warranty Management and Warranty Claims Support:
- Track warranties and support the client in filing and managing warranty claims.
- Post-Occupancy Evaluations and Feedback Surveys:
- Conduct post-occupancy walkthroughs to gather feedback and assess building performance.
- Recommend adjustments based on early operational issues.
- Support for Regulatory Compliance Inspections:
- Assist with preparation and documentation for any final inspections by regulatory bodies.
- Recommendations for Facility Maintenance Plans:
- Provide preventive maintenance recommendations for all major systems and equipment.
4. Deliverables:
- Final Inspection Reports with identified issues and recommended actions.
- Complete and verified Punch List Reports with rectification tracking.
- Full As-Built Documentation Package, including:
- As-Built Drawings
- O&M Manuals
- Equipment Warranties
- As-Built Drawings
- Training Manuals and Records of Facility Management Training Sessions.
- Warranty Tracking Logs and Claim Support Documentation.
- Post-Occupancy Evaluation Reports including feedback analysis and action plans.
- Preventive Maintenance Plan Recommendations.
5. Timeline:
- Project Kick-off and Initial Review: Week 0
- Site Inspections and Punch List Preparation: Weeks 1–2
- Coordination of Deficiency Rectification and Warranty Management: Weeks 3–4
- Client Staff Training and Documentation Handover: Week 5
- Post-Occupancy Support and Final Evaluations: Weeks 6–8
Site Logistic & Construction Scheduling
1. Site Layout and Logistics Planning:
- Design detailed site layout plans showing material storage, equipment zones, worker facilities, and access points.
- Plan efficient routes for vehicle movement, delivery management, and pedestrian access.
- Allocate space for temporary site offices, washrooms, security cabins, and first-aid units.
- Define emergency evacuation routes and fire-fighting equipment locations.
- Manage hoardings, signage, fencing, and site security arrangements.
2. Construction Activity Scheduling:
- Develop a comprehensive construction schedule using project management tools (Primavera, MS Project).
- Identify project milestones, activity dependencies, and resource allocation.
- Determine critical path activities to prioritize essential works.
- Create phase-wise work breakdown structure (WBS) to organize tasks.
- Update schedules periodically based on site progress and changes.

3. Material and Resource Coordination:
- Plan and coordinate the timely delivery of construction materials and equipment.
- Schedule unloading zones, storage methods, and material handling strategies.
- Align workforce mobilization with construction activities.
- Manage vendor schedules to avoid site congestion and delays.
- Monitor inventory levels and forecast material requirements.
4. Risk Management and Site Safety:
- Identify and mitigate risks related to logistics, site access, and construction activities.
- Integrate health, safety, and environmental (HSE) compliance into logistics and scheduling.
- Develop contingency plans for weather delays, delivery issues, and site emergencies.
- Conduct regular safety audits and inspections related to logistics management.
- Implement corrective actions for non-compliance or site disruptions.
5. Monitoring, Reporting, and Adjustments:
- Track site logistics performance and construction progress regularly.
- Prepare periodic reports highlighting scheduling updates and logistic adjustments.
- Conduct site meetings with contractors and stakeholders to review progress.
- Recommend adjustments in site layout or activity sequencing as needed.
- Support in closing logistics facilities during demobilization and project closeout.
Quality Assurance & Quality Control (QA/QC) Programs
1. Development of QA/QC Plans:
- Create a comprehensive Quality Assurance and Quality Control program tailored to project requirements.
- Define quality objectives, standards, and project-specific benchmarks.
- Establish roles and responsibilities for QA/QC management across all teams.
- Develop Inspection and Test Plans (ITPs) for major construction activities.
- Ensure alignment of QA/QC plans with industry standards (ISO, ASTM, project specs).
2. Quality Assurance Implementation:
- Conduct pre-construction QA meetings with client, contractors, and vendors.
- Review and approve project materials, equipment, and construction methodologies.
- Implement document control systems to track submittals, approvals, and revisions.
- Perform regular audits on contractor quality systems and processes.
- Establish preventive measures to avoid quality issues before they occur.

3. Quality Control Activities:
- Perform routine field inspections, testing, and verification during construction.
- Monitor workmanship, materials, and installation methods against approved standards.
- Coordinate third-party testing agencies for specialized quality tests.
- Issue Non-Conformance Reports (NCRs) and ensure timely corrective actions.
- Maintain detailed inspection reports, photographic records, and test certificates.
4. Risk Mitigation and Compliance Monitoring:
- Identify potential quality risks and implement mitigation strategies early.
- Verify compliance with local building codes, regulations, and client specifications.
- Conduct root-cause analysis for recurring quality issues and recommend solutions.
- Implement continuous improvement measures throughout the project lifecycle.
- Support regulatory inspections and certifications as required.
5. Reporting, Handover, and Training:
- Prepare Weekly and Monthly QA/QC Progress Reports.
- Compile final Quality Documentation including inspection records and testing results.
- Assist with punch list development, tracking, and closure verification.
- Deliver QA/QC training sessions for contractors and client teams.
- Support the final handover process by ensuring all quality requirements are met