Resource Allocation & Optimization
Human Resource Hiring and Allocation
1. Workforce Planning & Strategy
- Conduct workforce gap analysis to identify hiring needs
- Define job roles, responsibilities, and competency frameworks
- Develop resource allocation models (FTE, contractors, outsourcing)
- Align hiring plan with project timelines and budget constraints
2. Talent Acquisition & Recruitment
- Prepare job descriptions and candidate screening criteria
- Manage end-to-end recruitment (sourcing, interviewing, selection)
- Coordinate with HR teams, agencies, and job portals
- Ensure diversity & compliance in hiring practices
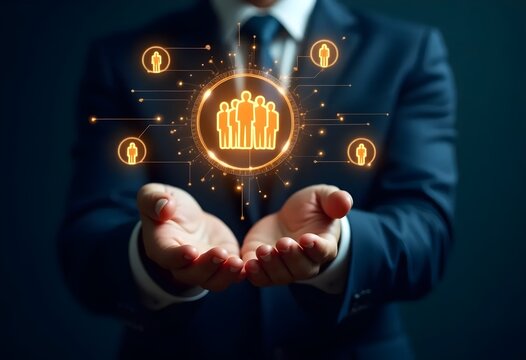
3. Skills Assessment & Onboarding
- Conduct technical & behavioral assessments for role fit
- Design onboarding programs for smooth integration
- Provide training needs analysis for upskilling
- Implement probation review mechanisms
4. Resource Allocation & Deployment
- Create staffing plans by project phase/department
- Optimize team structures (hybrid, remote, on-site)
- Monitor workload distribution to prevent burnout
- Manage cross-functional resource sharing
5. Performance Tracking & Retention
- Establish KPIs for productivity & quality
- Implement employee engagement initiatives
- Conduct exit interviews & turnover analysis
- Recommend retention strategies
Construction equipment (Rental hiring) Consultation
1. Equipment Needs Assessment & Planning
- Conduct project requirement analysis to determine equipment types (excavators, cranes, loaders, etc.)
- Evaluate project timelines to optimize rental durations
- Assess site conditions (terrain, space, access) for equipment suitability
- Develop cost-benefit analysis (rent vs. buy)
2. Vendor Selection & Contract Negotiation
- Identify reliable rental suppliers with verified equipment quality
- Compare rental rates, terms, and conditions across vendors
- Negotiate favorable contracts (rates, maintenance, insurance, penalties)
- Ensure compliance with safety and regulatory standards
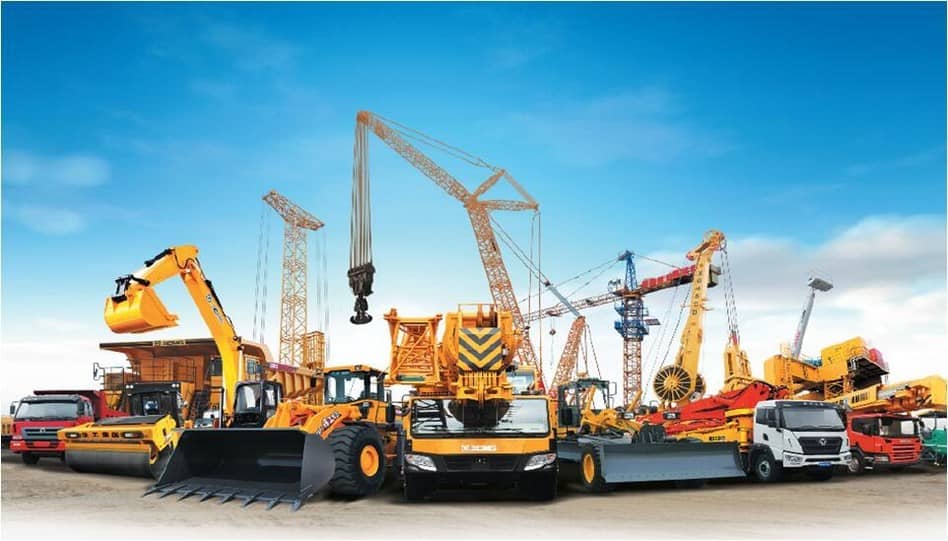
3. Equipment Allocation & Logistics
- Create equipment deployment schedules aligned with project phases
- Coordinate transportation & on-site delivery
- Manage fuel, maintenance, and operator arrangements
- Track equipment utilization & idle time
4. Performance Monitoring & Cost Control
- Implement equipment tracking systems (GPS, telematics)
- Monitor operational efficiency (downtime, productivity)
- Control rental cost overruns with real-time budget tracking
- Optimize equipment sharing/swapping between projects
5. Risk Management & Compliance
- Verify equipment certifications & inspection records
- Ensure operator licensing & safety training compliance
- Manage breakdowns & replacements with minimal downtime
- Handle insurance claims & liability issues
Construction equipment (Purchase) Consultation
1. Equipment Needs Assessment & Planning
- Conduct project requirement analysis to determine optimal equipment types and specifications
- Perform cost-benefit analysis (purchase vs. lease vs. rent)
- Evaluate project timelines to determine equipment utilization periods
- Assess site conditions (terrain, climate, space constraints) for equipment suitability
2. Market Research & Vendor Selection
- Identify reputable manufacturers and dealers (new/used equipment)
- Compare equipment models, features, and pricing across brands
- Analyze total cost of ownership (TCO) including maintenance and resale value
- Shortlist most suitable vendors based on reliability and after-sales support
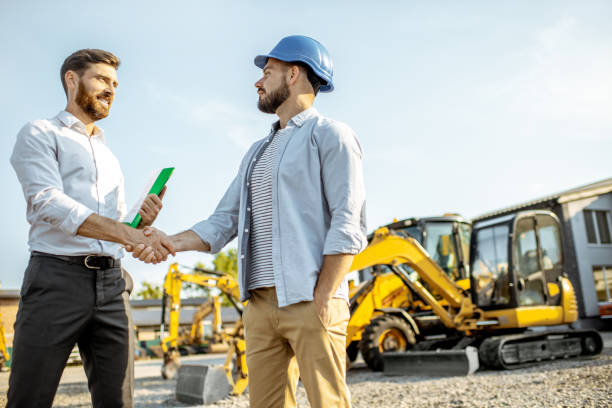
3. Procurement Strategy & Negotiation
- Develop equipment procurement plan aligned with project cash flow
- Negotiate purchase terms, warranties, and payment schedules
- Arrange equipment demonstrations and testing
- Secure financing options (if required) and evaluate loan/lease terms
4. Purchase Execution & Logistics
- Manage purchase order documentation and contracts
- Coordinate shipping, customs clearance, and delivery
- Oversee equipment inspection and acceptance
- Handle registration, insurance, and compliance documentation
5. Post-Purchase Support & Optimization
- Develop preventive maintenance schedules
- Recommend operator training programs
- Monitor equipment performance and ROI
- Provide resale/disposal advisory when equipment reaches end-of-life